BLUEFISH
PROGRAM
Optical
systems used to steer robots are commonplace. Advanced robot kits are available
from toy shops that avoid each other. The challenge is to use the technology to
steer a ship in open water away from other vessels to avoid collisions. It
all comes down to the quality of your sensors, speed of processing and the
sophistication of algorithms used when programming. The Bluefish development
hull will be tested at various levels of sophistication - starting at the
beginning with sensors used in off the shelf toys, then replacing them with
increasingly advanced sensors and processing ability, until we have a system
that is suitable for commercial shipping. That
system will then be fitted to the full size prototype ship and sailed in all the
busiest shipping lanes to prove that robot ships can be fully autonomous. Please
get in touch with us if you would like to
contribute to such a program.
OMRON
FAST COMPACT VISION SYSTEM - AUGUST 2013
With
a high-speed image bus, four-core processing, a new and efficient vision
algorithm and fast EtherCAT communications, the new FH compact vision system
from Omron is believed to be the fastest compact vision system on the market.
Designed
for fast efficient operation at every stage from image capture to data output,
Omron’s new FH vision systems are specifically intended for seamless
integration with PLCs, motion controllers and robotic control systems, and are
ideally suited for applications in high-speed manufacturing machines of all
types.
A further benefit is that FH vision systems are fully compatible with Omron
Sysmac Studio Automation software.
This means that only one software
package is needed to set up all of the major components used in an automation
system, which greatly reduces the amount of work involved in machine design.
Sysmac Studio can be used to set up, debug and simulate all slave devices
connected via EtherCAT, including not only vision and other sensing elements,
but also motion controllers, logic devices and drives.
At the heart of the new FH vision controllers is Omron’s innovative Shape
Search III vision algorithm. Up to nine times faster when carrying out searches
than conventional algorithms, Shape Search III allows fast, precise measurements
to be made even if images are out of focus, or if the targets are randomly
positioned, randomly rotated or overlapping. This exceptional performance is
achieved without the need for user-dependent calibration, which means that FH
vision systems are particularly easy to set up and operate.
Because of their exceptionally efficient image handling characteristics, the new
vision systems can support multiple high-resolution cameras with no degradation
of performance or image capture speed. This allows them to handle even the most
complex of inspection tasks and, in some applications, it also means that a
single vision controller can be used where previously several would have been
needed, which makes possible substantial cost savings.
To ensure straightforward and dependable integration with all types of
automation and control system, Omron FH compact vision controllers incorporate
support for the EtherCAT machine control network. This allows communications
cycle times as short as 500µS to be achieved as well as allowing the
implementation of motion
control synchronised with the communication cycle. The controllers also
support custom.NET controls, which mean that images and measurement results can
be readily displayed on an external PC.
JANUARY
2013 Vision sensor is set to shake up the inspection market - Omron's new FQ2
vision sensor sets a new standard for performance and flexibility, providing
functionality not previously available in a vision sensor format.
The
FQ2 provides complete flexibility, with over 60 hardware options including fully
integrated cameras with high brightness illumination to C-Mount lens cameras,
colour and monochrome cameras, as well as high resolution types for accurate
inspection. Even, units specifically designed for OCV (Optical Character
Verification) and barcode verification applications are also available. Whatever
your application, there is an FQ2 which fits perfectly.
The FQ2 inspection tool library is now without compromise, as standard 9
inspection items including Omron’s coveted “Shape Search II”, shape based
inspection tool, which provides 10x speed and ultra-high accuracy detection.
Using “Real Colour” inspection algorithms, the FQ2 processes images in a
similar way to the human eye. High stability is achieved, yet set-up is
simplified by negating the complex process of manually setting digital colour
filters, which is required on most other systems.
Advanced character verification of printed text, such as date codes and lot
codes is now possible on the FQ2 platform. The set-up task has been simplified
to allow easy deployment, through pre-set character libraries, set-up can be
completed in seconds and without the need for in-depth knowledge of vision
technology.
Stable inspection is guaranteed, with the FQ2’s crystal clear image
capability. High performance lighting,
HDR processing, polarising filters and a new suite of digital image filters, all
ensure the FQ2 provides the best possible image, improving the stability and
reliability of your application.
Integration couldn’t be easier; the FQ2 supports TCP/IP, EtherNet/IP and PLC
Link as standard, ensuring seamless communication without any effort. Up to 32
cameras can be networked together, providing a single interface point for
machines which need multiple inspection zones. As standard, 3 digital outputs
are provided, although this can be increased through an I/O expansion module to
23 outputs, vastly increasing the number of viable applications.
High performance and simple operation, the FQ2 is the perfect choice for all
your inspection needs.
Omron has been developing and manufacturing machine vision products for over 30
years and has been recognised as the global Number One for machine vision sensor
products according to the World Market for
Machine Vision – 2012 Edition report from independent market research
company, IMS Research.
Omron
Electronics
Opal
Drive
Fox Milne
Milton Keynes
MK15 0DG
United Kingdom
Telephone
: 01908 258 258
Fax : 01908 258 158
Email : uk@eu.omron.com
Web : www.industrial.omron.co.uk
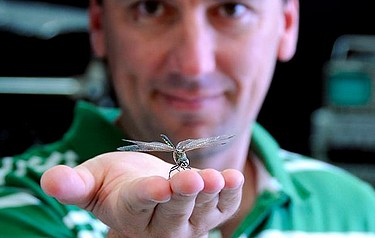
AUGUST
2013 DRAGONFLY SIGHT - A study of dragonfly
sight may advance artificial vision systems. Researchers have discovered a novel
and complex visual circuit in a dragonfly's brain that could one day help to
improve vision systems for robots.
Dr
Steven Wiederman and Associate Professor David O'Carroll from the University of
Adelaide's Centre for Neuroscience Research have been studying the underlying
processes of insect
vision and applying that knowledge in robotics
and artificial vision systems.
Their latest discovery, published this month in The
Journal of Neuroscience, is that the brains of dragonflies combine
opposite pathways - both an ON and OFF switch - when processing information
about simple dark objects.
"To perceive the edges of objects and changes in light or darkness, the
brains of many animals, including insects, frogs, and even humans,
use two independent pathways, known as ON and OFF channels," says lead
author Dr Wiederman.
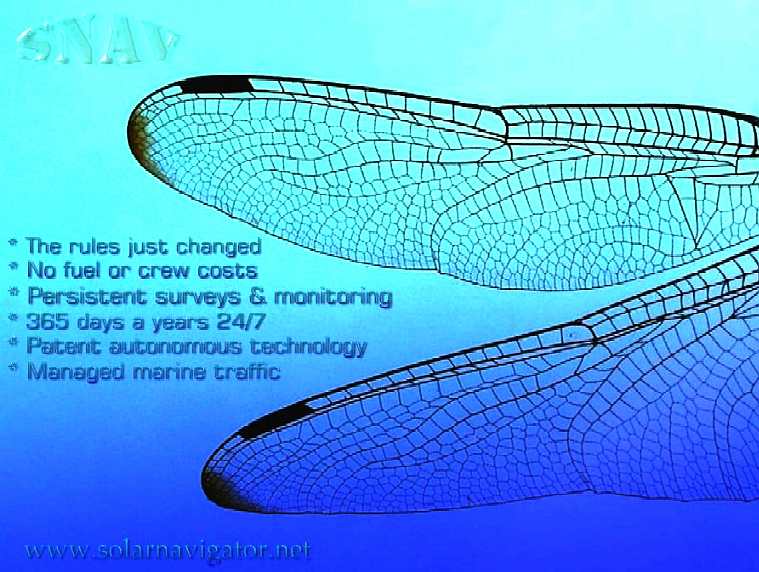
"Most animals will use a combination of ON switches with other ON switches
in the brain, or OFF and OFF, depending on the circumstances. But what we show
occurring in the dragonfly's brain is the combination of both OFF and ON switches.
This happens in response to simple dark objects, likely to represent potential
prey to this aerial predator.
"Although we've found this new visual circuit in the dragonfly,
it's possible that many other animals could also have this circuit for
perceiving various objects."
The researchers were able to record their results directly from
'target-selective' neurons in dragonflies' brains. They presented the
dragonflies with moving lights that changed in intensity, as well as both light
and dark targets.
"We discovered that the responses to the dark targets were much greater
than we expected, and that the dragonfly's ability to respond to a dark moving
target is from the correlation of opposite contrast pathways: OFF with ON,"
Dr Wiederman says.
"The exact mechanisms that occur in the brain for this to happen are of
great interest in visual neurosciences generally, as well as for solving
engineering applications in target detection and tracking. Understanding how
visual systems work can have a range of outcomes, such as in the development of
neural prosthetics and improvements in robot vision.
"A project is now underway at the University of Adelaide to translate much
of the research we've conducted into a robot, to see if it can emulate the
dragonfly's vision and movement. This project is well underway and once
complete, watching our autonomous dragonfly robot will be very exciting,"
he adds.
JANUARY
2013 FLIR INFRA RED VISION
Infrared
machine vision - no need for visible light, FLIR thermal machine vision brings
many benefits but perhaps the most significant is its ability to do the job
without the need for additional lighting.
The
result is a simple and efficient system whose reliability exceeds that of
traditional vision systems. It also provides greater intelligence in the
automated environment, such as confirming cure temperatures that may have a
bearing on product quality.
The new, uncooled FLIR A65 typifies this capability and, in addition, factors in
extremely small physical size and high image quality. It is the ideal
choice for manufacturers seeking a discrete, high resolution vision system at an
affordable price. Integration into existing production systems is quick
and easy thanks to a range of in-built connectivity options.
This top of the range FLIR A series camera produces crisp thermal imaging from
640 x 512 pixels in the temperature range -40?C to +550?C. This image quality is
particularly useful where small differences of thermal contrast need to be
detected; its rated sensitivity is <50mK.
In common with all FLIR automation cameras, the FLIR A65 is able to provide the
same performance through steam, smoke and in complete darkness. Multiple
FLIR A65 cameras
can be synchronised whereby one is configured as the master and additional units
as slaves. This model also offers the choice of a 13mm or 25mm fixed focus
lens.
The FLIR A65 is GigE Vision compatible. This is the camera interface
standard, developed using the Gigabit Ethernet communication protocol to allow
fast image transfer using low cost standard cables over long distances.
GeniCam support is also provided, a generic programming interface for quick and
easy set up. Importantly, this protocol allows the FLIR A65 to use third
party software
such as IMAQ Vision and Halcon.
The standard FLIR Tools software that is supplied with the camera enables
thermal images to be viewed and analysed and includes functions such as time
versus temperature plots.
Users that require greater functionality and the ability to record images can
choose FLIR Tools+.
Flir
Systems
2
Kings Hill
West Malling
Kent
ME19 4AQ
United Kingdom
Telephone
: 01732 220011
Fax : 01732 220014
Email : sales@flir.uk.com
Web : www.flir.com/thg
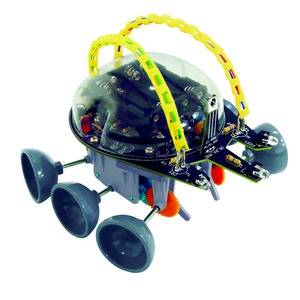
An
inexpensive educational robot toy kit from Maplins Electronics that uses optical
recognition (infra red) sensors and a microchip to calculate how to avoid
objects
LINKS http://www.maplin.co.uk/ http://www.dpaonthenet.net/article/55506/Infrared-machine-vision-no-need-for-visible-light.aspx http://www.dpaonthenet.net/article/55396/Vision-sensor-is-set-to-shake-up-the-inspection-market.aspx Dragonfly
sight may advance artificial vision systems http://www.dpaonthenet.net/article/60347/Omron-launches-fast-compact-vision-system.aspx
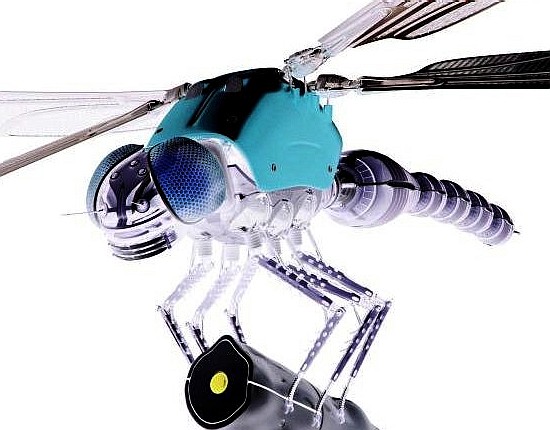
The SNAV
platform, under development via the Bluefish program, is a robotic ocean
workhorse and the largest
solar vessel design in the world. Based on a stable
SWASH
hull this design is the prototype for fast zero carbon ocean transport of
the future. The robot
ship uses no diesel fuel to monitor the oceans autonomously (COLREGS
compliant) at relatively high
speed 24/7 and 365 days a year - only possible with the revolutionary energy harvesting system. This vessel
pays for itself in fuel saved every ten years.
|